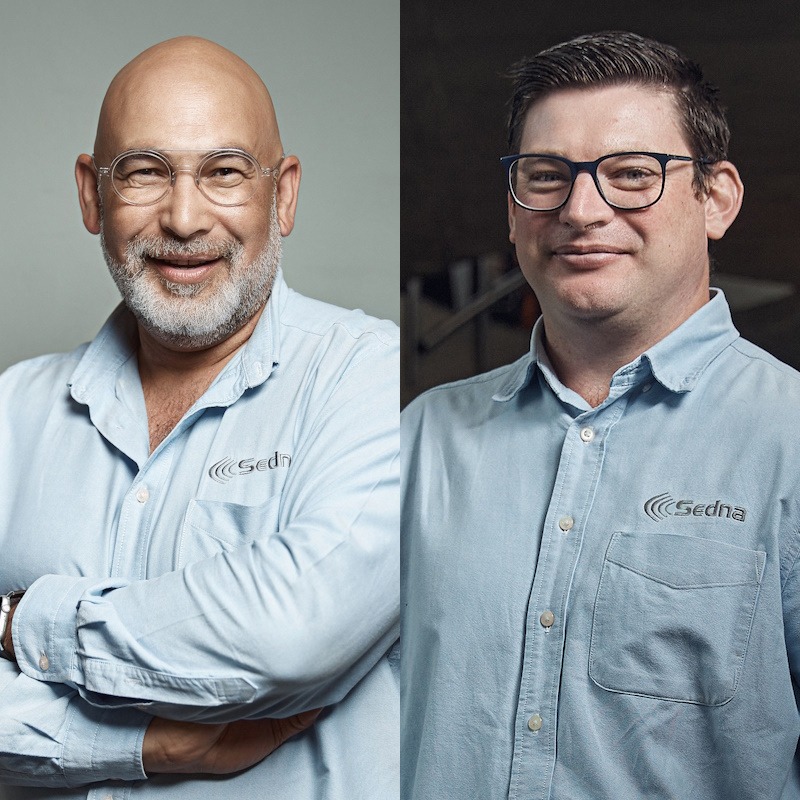
Tech disruption in the mining and heavy-duty industrial sectors in Africa is set to continue at pace, forcing operators to adapt to change or face greater risk to their workers and bottom lines.
While the trend until now has been for many of Africa’s industrial users to take smaller steps towards digital solutions like integrated communication systems and the connected worker, there is a need to ramp up progress to enhance efficiency and safety.
With inflation, load-shedding, volatility and political risk all weighing down sentiment and the ability to expand, companies in Africa must accelerate change. Based on recent moves seen in Europe and North America, we can expect this gap to close steadily as companies see the benefits and amplify the use cases of high tech into more areas of their operations, but especially on their networks to enhance speed, stability and innovation on the connected or autonomous worker and safety fronts.
On the rollout of Collision Avoidance Systems (CAS) (which can go up to CAS level 9), for instance, many companies are making important strides, getting to levels 6 or 7 and with the aim of switching on the full service in time. These systems will see machines issuing warnings to avoid collisions on site. It creates zones around equipment and can even shut down or stop assets before an incident occurs.
However, for this to work - even if it is switched on in increments - is to have the infrastructure in place to allow for a seamless rollout. This must happen together with enhanced networks that work well in real time, whether you are below or underground.
But once implemented, the results speak for themselves. For one, companies will have a rich source of data at their fingertips to create efficiencies, cost savings and improve their safety records. When combined with dedicated network solutions, companies can see traffic on networks drop by about a third, saving time, money and avoiding the hassle factor. In a case study we were involved in, an asset using normal Wifi at a distance of about 130m, produced an uplink of 8 mbps. However, when placed on a private LTE network, the load dropped significantly to just 3 mbps. With an unacceptably high number of fatalities still occurring through machine to person or person to person communication, these solutions will go a long way to making sites safer for everyone and greatly enhance the ability of companies to grow and focus on their core capabilities.
Private LTE networks offer an added layer of end-to-end reliability, security and efficiency and work by using 4G radios to connect to smart devices and routers. It is especially beneficial for heavy duty miners and industrial users seeking automated and communication solutions. It has been shown that problems on a site, like automated communication for a truck fleet, can be reduced by over 80% after switching to pLTE, while significant cost savings (you don’t need nearly as many pLTE radios than you do WiFi radios) are also being achieved by many companies, like a 90% drop in “stop” events.
Due to the immense benefits and growing demand for pLTE, Sedna has ramped up its private wireless partnership with Nokia, including the deployment of the Nokia Digital Automation Cloud (DAC) to expand further into southern Africa and other Industry 4.0 applications.
This comes as demand for enhanced network solutions grows in Africa thanks to their ability to deliver productive solutions in operational areas above and underground.
That being said, does this mean machines are coming to take over the jobs of humans on mines and at factories? Not at all, but once these solutions are switched on, they will connect workers and bring about far more efficiency. It’s a win-win.
What we can expect going forward is to see AI being layered more into worker safety solutions because automation has such a massive safety upside.
Share