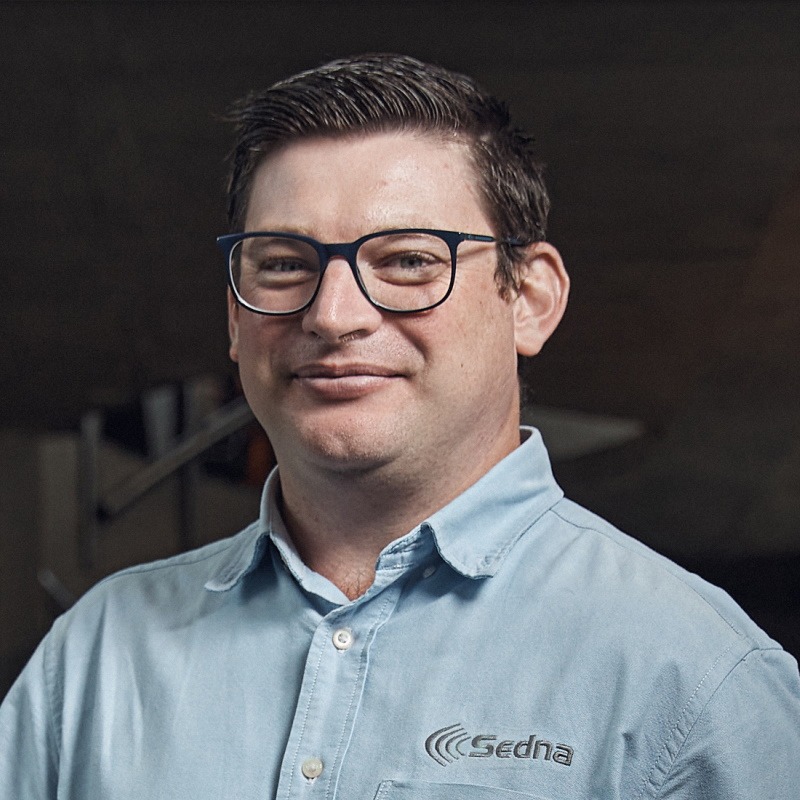
Operational technology (OT) governance is no longer a nice to have, but a business imperative for Africa’s mines and heavy-duty industries as risks to operations and lives increase. Going forward, digital solutions that drive integration and continuity while keeping workers safe and protecting against cyber threats will only rise in prominence as mines and manufacturers, which remain integral to Africa’s future growth, grasp the benefits of the connected, integrated digital world.
As a leading digital solution provider in the mining and industrial sector in EMEA we are at the forefront of these changes and are pleased to report that new business requests are increasing early in 2024 as more businesses look to drive change that will grow operations, save costs and protect workers and OT systems from threats. Following the recent mining indaba in South Africa and our road showcases o numerous mines and heavy-duty companies early in the new year, we can say that demand is already picking up for these solutions in Africa – though a lack of awareness and cost concerns remain hurdles.
African mines are, of course, under immense pressure on many fronts, with port backlogs and load shedding adding to the burden. It is critical they see real value early on in their journey towards scalable and reliable connectivity. Our approach is, therefore, to first conduct a comprehensive audit so that we can understand, analyse with and build on existing systems without reinventing the wheel. Enabling Industry 4.0 revolution within the OT environment of heavy industries, improves the onboarding of new OT solutions seamlessly without compromising security and uptime requirements. It also shows enhanced turnaround times on successful results from business-critical systems within the respective business ecosystem.
The benefits will be immense the more mines and heavy industry follows an Industry 4.0 adoption model. The Syama mine in Mali is a good example of how integrated systems lead to major savings and improved outcomes. In 2015, Resolute Mining took over operations at Syama and transformed it into the world’s first purpose-built automated mine. Employees use a fiber-optic network connected to above-ground control centers to manage and monitor all activities, from the clearing of the drill point to extraction, loading, and hauling. Although the initial investment was steep, according to Brookings, the changes are expected to cut mining costs by 30 percent and improve overall efficiency. The machines can operate 22 hours a day, and there is no time lost due to shift changes.
The key is to make this happen more broadly across both mines and heavy-duty industries in Africa. The solution architecture should never just be about adopting the latest and greatest new tech or app, but ensuring operational readiness throughout an organisation. Part of taking the industry on this journey is raising awareness – many do not yet fully understand how automation or OT fits into what they have – but once the benefits become clear, we find that companies are champing at the bit to integrate.
McKinsey estimates that innovations in artificial intelligence (AI), machine learning and Internet of Things have the potential to save the mining sector an estimated $373 billion by 2025 by automating machinery operation, facilitating predictive maintenance, improving traceability, harnessing the power of real-time data and analytics, and providing visibility across the mine-to-market value chain. The problem is worldwide mining operations are as much as 28% less productive than they were a decade before, says the report.
Science Direct highlights that a lot of moves are taking place globally to drive safety using tech, buttressed by policy. For instance, the Canadian government has laid a plan to fully automate a mine in the Northern region by 2050, which will be controlled remotely using satellite imageries. Canadian Stobie underground nickel mining company already operates using automated machinery such as drill rigs, scrappers, and haul trucks, all controlled from a control room. Sweden has established the Grountecknik 2000 strategic plan whose main goal is to promote safety and productivity through automation in mining. Australia's Commonwealth Scientific and Industrial Research Organization is determined to attain intelligent mining, especially in underground settings, to promote safety and production rates.
There is little doubt that this is a trend we will see taking shape and being embedded more and more in Africa over the coming years. Fortunately, we have the technology and expertise to make this happen.
According to Brookings, to unlock mineral-rich African countries’ full potential, mining companies and African governments must embrace Fourth Industrial Revolution (4IR) technologies. Artificial intelligence (AI), automation, and big data can help mining firms limit environmental damage, improve working conditions, reduce operating costs, and boost productivity.
We believe this is all in reach for Africa, which is not behind the curve. In our view, proper OT governance architecture is a proactive intelligence platform that will add significant value to all layers within a mining or industrial operation. Unlocking key data from a central location and distributing it to whoever needs to use it to make the best decision for the business and its workers is the gold dust that will make Africa’s mines thrive. The only question is how fast they hit the “on” button.
Share